A lot of linear processes go into the making of cars. And for that, manufacturers turn to linear actuators. So, these motion devices form an essential component of car manufacturing. It’s not wrong to say there’s a linear actuator in every modern car.
Besides being essential, the actuators also have helpful benefits. They improve the safety, quality, and efficiency of vehicles. This post will explain how linear actuators help ease the car manufacturing process.
Here are three main aspects where it’s applied:
-
Assembly
While assembling car parts, manufacturers use linear actuators for automation and optimization. Consider the car doors and windows, for example. These parts slide up and down and open in and out. In other words, they perform straight movements, and depend on linear actuators to work.
Another top application of linear motion devices during assembly is for the chassis. Most car chassis come with a robotic weld gun, set up using linear actuators. There are also devices intended for smaller parts, like printed circuit boards for the control panel. The devices will ensure repeatability, thereby lessening the chances of errors.
Linear actuators also play a part in setting up the engine. A good example is the arrangement of cylinders via boring and honing. Such applications need precise drilling and finishing. And linear motion devices make it easy, thanks to their high speed and accuracy.
Furthermore, manufacturers also need to link the engine and chassis parts. To do that, they use screws and bolts, and rivets, to name a few. They also need linear actuator devices to ensure smooth and accurate motion.
-
Testing
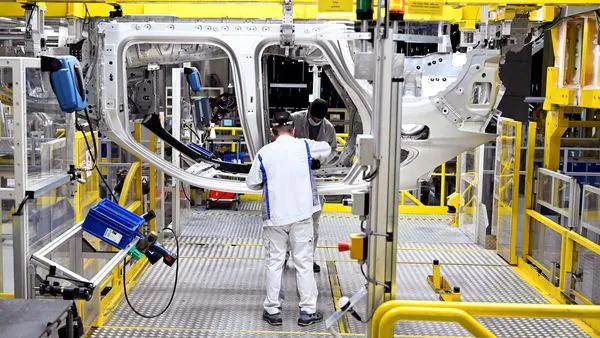
Source: auto.hindustantimes.com
Before releasing a vehicle to the public, manufacturers must measure its overall performance. Simply put, they must test the car. Since many car operations are linear, actuators are usually the go-to for this testing.
For instance, manufacturers use linear actuators to test parts like brakes, steering, PCB assembly, and suspension. The devices are dependable for such as they simulate adverse situations. For example, actuators can simulate vibrations and rugged environments.
A more practical application of linear actuators in testing is measuring tension. Consider the car seat, for example. A manufacturer can check how it holds up against different loads and forces. Again, a linear actuator can simulate the conditions.
Powertrain testing is another area where actuators come into play. The car parking locks, gear shifts, and clutches, among others, all need checking. Thanks to linear motion devices, manufacturers can assess the efficiency of these parts.
-
Accessibility
Accessibility has to do with convenience. So, when you sit in a car and find it comfortable, know that linear actuators helped. Manufacturers construct car seats, doors, trunks, and windows using motion devices.
When in a car, you can adjust the seat to different heights and angles. How is that possible? It’s because linear actuators installed during manufacturing eases the process. The same applies when you adjust the headrest or open and close doors and windows.
Conclusion
Car manufacturers use linear actuators to:
- Assemble various components
- Test performance and efficiency
- Enhance accessibility for users
This means the motion devices ensure the car parts are well-fitted, work optimally, and that the end user feels comfortable.